Ultrasonic Testing
- Uses high frequency sound waves that create a signal or image showing the inside of the vessel
- Thickness measurement is used to gauge the remaining life of a pipe or tank
- There are other methods such as pulse echo, time-of-flight diffraction, and shear wave, that measure sound waves and create 3D images of the internal structure
- Useful for metallic and composite parts
- Helps find cracks, voids, delamination, and other issues
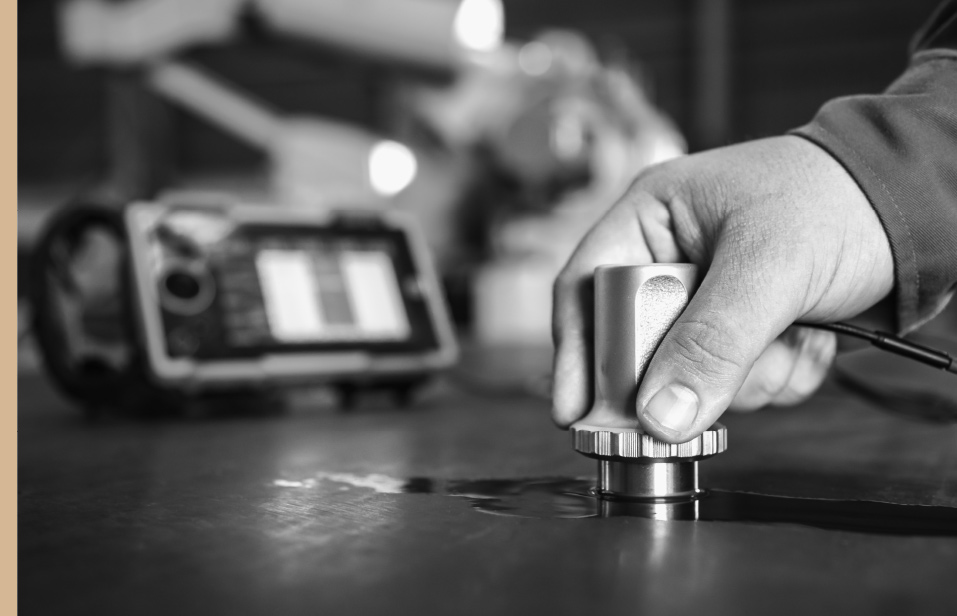
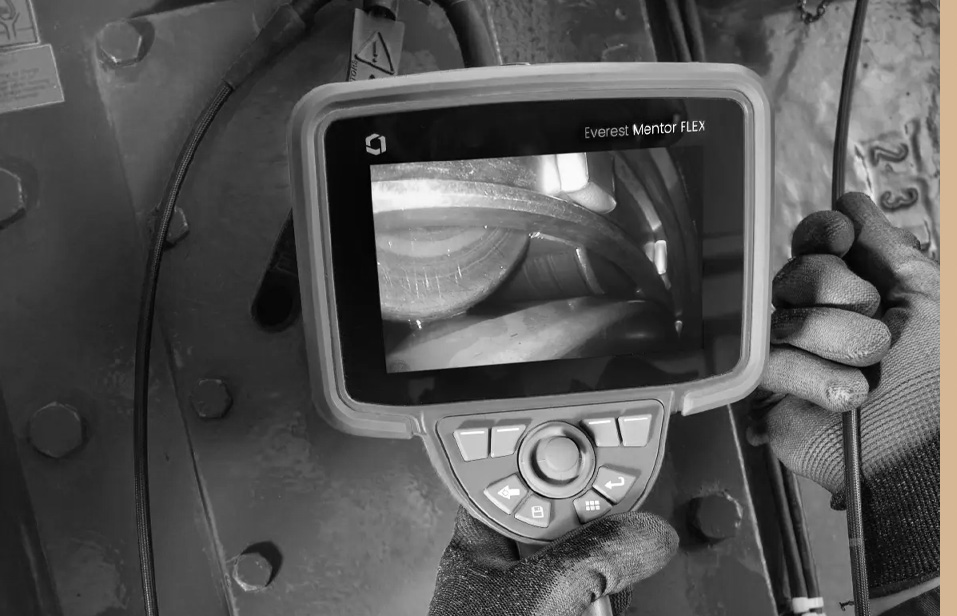
Visual or Optical Testing
- Utilizes different types of cameras to examine inaccessible areas
- Cameras may be mobilized, waterproof, or flexible
- Allows safe inspection in spaces that might be dangerous, radioactive or toxic
- Can spot imperfections, dislocations, leaks, corrosion, pitting, cracking, or obstructions
- The main categories of VT include microscopy, fiberscopes, borescopes, crawlers, pan-tilt-zoom (PTZ) cameras
Magnetic Particle Testing
- Executed by creating a magnetic field in a ferromagnetic material and covering the excited part with iron particles
- Particles may be dry or suspended in a fluid
- Finds defects in the surface like voids and cracks using magnetic technology
- Makes it easy to see cracks and other defects the naked eye cannot see
- Identifies cracks, pits, and voids
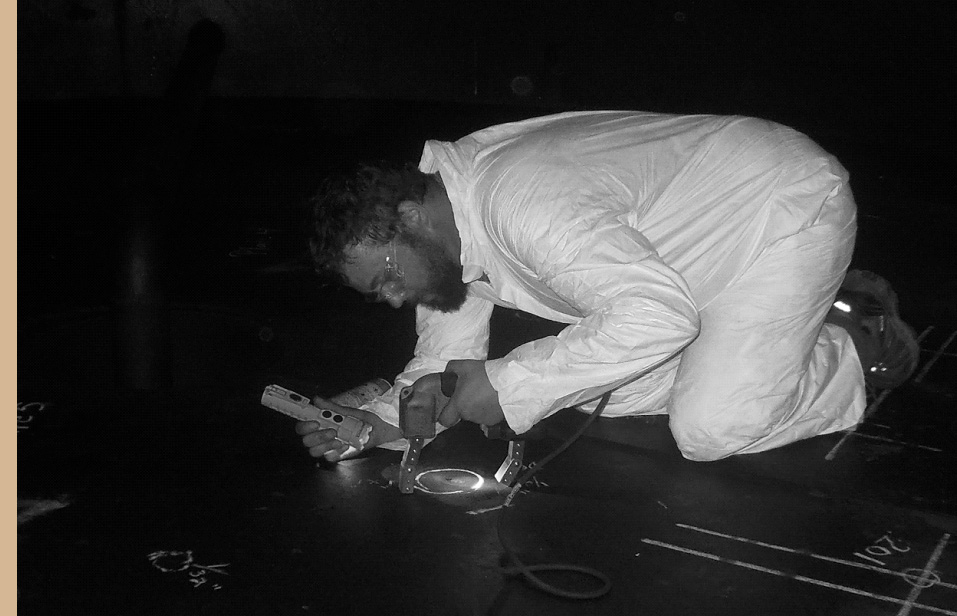
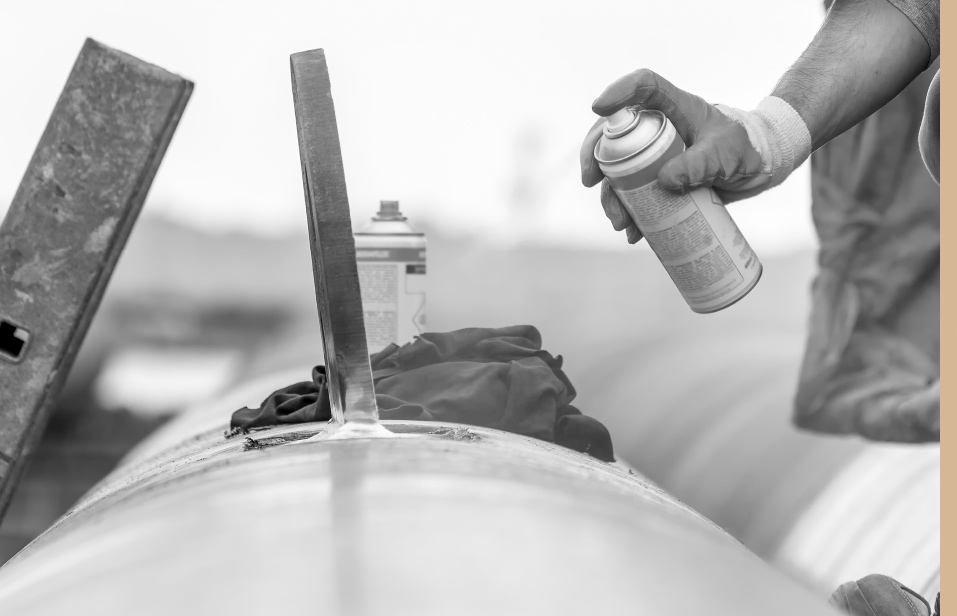
Penetrant Testing
- Find issues in parts that are not visible by eye
- Utilizes both visible and fluorescent dye
- A part is coated with the fluorescent dye and then wiped clean, then a developer is applied to the surface
- The UV lamp shows where excess dye remains in cracks and voids on the surface, making it easy to see with the eye
Electromagnetic Testing
- Takes advantage of the fact that rapidly changing the magnetic field around a metallic part creates electrical currents in the part
- Currents are disrupted by indications like cracks and voids; measuring these electrical currents allows the measurement of defects within the part
- Allows for the identification or classification of materials
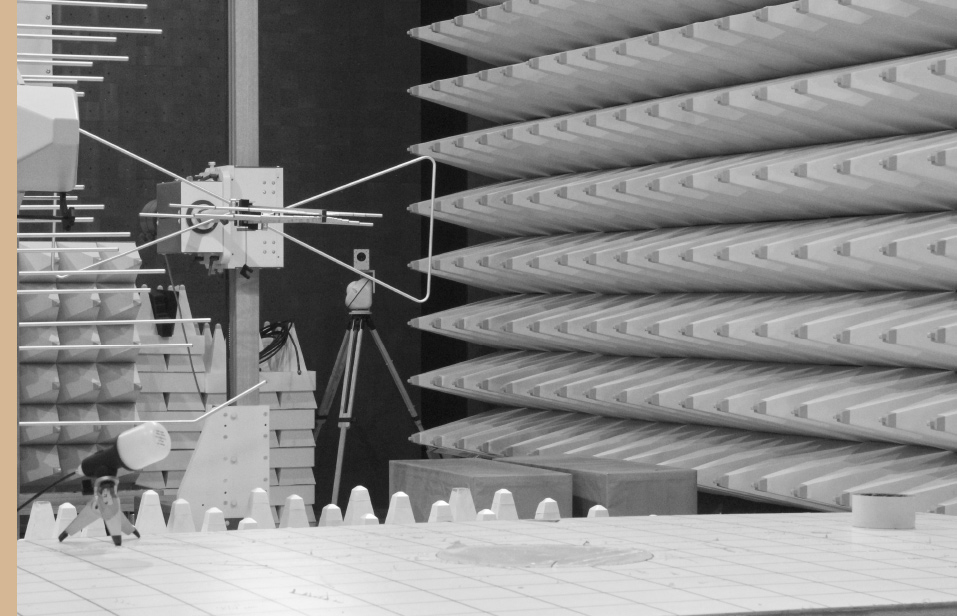
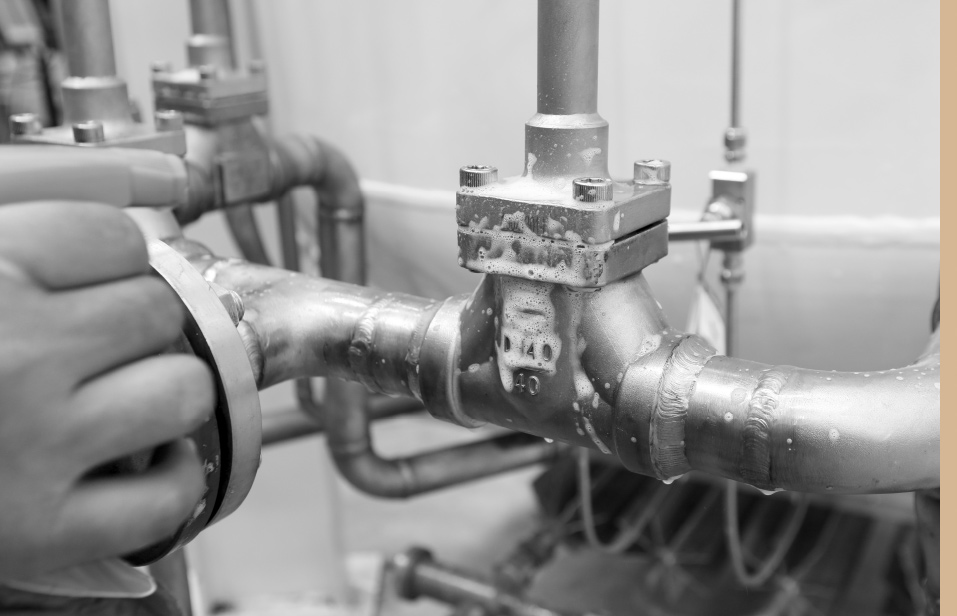
Leak Testing
- Used extensively in industry, construction, and municipal infrastructure
- Ensures the safety of gas lines, boilers, oil pipelines, and other high-pressure and hazardous material storage applications
- Techniques include methods that provide a go/no-go evaluation of a system
- Tanks and vessels are tested by being filled with water and adjusted to operating pressures; the water prevents dangerous and catastrophic failure should the test fail
- Soap bubble testing is used on installed gas lines to see small gas leaks on lines
- For hydrogen gas lines, electronic sniffing and sampling devices are often used
- Vacuum box testing is used on the tank floor and chine weld to detect any leakage.